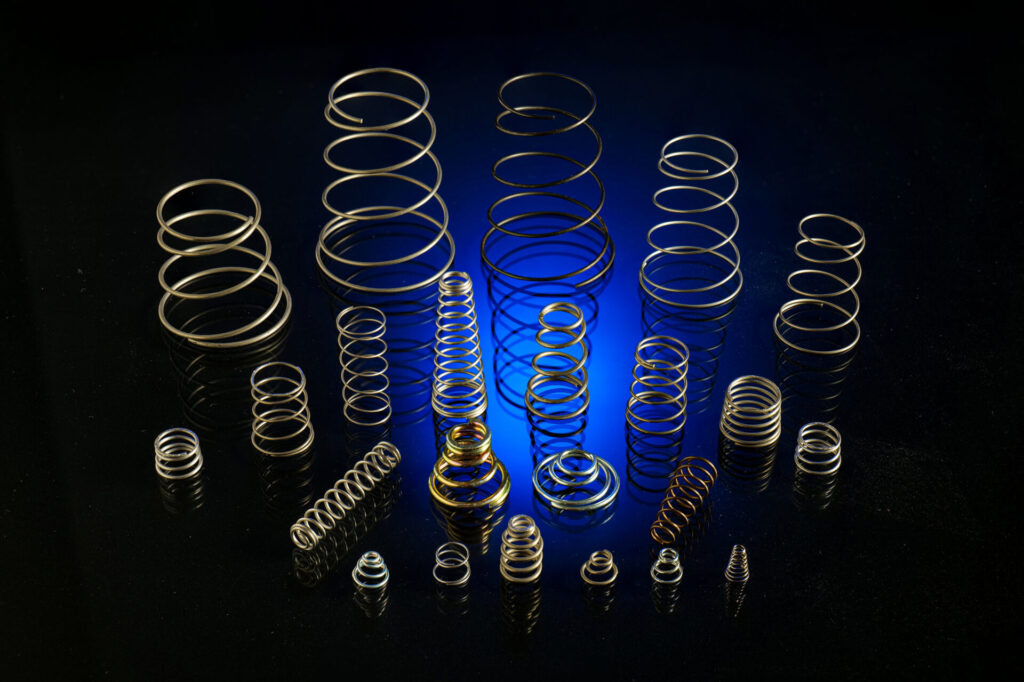
Conical springs
Manufacturing Process of Conical Spring :
The process of conical spring manufacturers requires specialized equipment and techniques to achieve the desired tapered shape and consistent performance.
Material Selection :
- Conical springs are typically made from high-quality spring materials such as music wire, stainless steel, or high-carbon steel.
- The choice of material depends on factors such as required strength, resistance to corrosion, and the application environment.
Wire Forming :
- The process starts with a coil of wire that is fed into a specialized machine.
- The wire is then formed into the initial coils of the conical spring, typically with a larger diameter at one end and a smaller diameter at the other.
- CNC (Computer Numerical Control) machines are often used for precise shaping and consistency.
Heat Treatment :
- After the initial forming, the conical spring undergoes heat treatment to improve its mechanical properties.
- Heat treatment involves heating the spring to a specific temperature and then cooling it at a controlled rate to set its shape and enhance its strength.
Coiling and Tapering :
- The next step involves coiling the wire further to achieve the desired tapering effect.
- Specialized machines are used to gradually reduce the diameter of the coils along the length of the spring, creating the conical shape.
- This process requires precise control to ensure uniform tapering and consistent spring rates.
End Grinding :
- Once the conical spring is formed, the ends may be ground to achieve flat surfaces or specific shapes.
- Grinding ensures proper seating and alignment of the spring in its application, as well as enhancing its appearance.
Shot Peening(Optional):
- Shot peening can be used to improve the fatigue life and durability of the conical spring.
- This process involves bombarding the surface of the spring with small, spherical particles to induce compressive stresses.
Finishing :
- conical springs manufacturers may undergo additional finishing processes based on application requirements.
- This can include coating or plating for corrosion resistance, painting for identification or aesthetics, or passivation for improved surface properties.
Quality Control :
- Throughout the manufacturing process, stringent quality control measures are implemented.
- Dimensional measurements, load testing, and fatigue testing are performed to ensure that each conical spring meets the required specifications.
Using Conical Springs
Conical spring manufacturers offer several advantages due to their tapered shape and variable spring rates, making them suitable for a range of applications
Automotive Suspension
Conical springs are used in vehicle suspension systems to provide a progressive spring rate.They offer a softer initial response for comfort while providing increased stiffness as the spring is compressed further for stability during cornering.
Aerospace Applications
Conical springs find use in aerospace for landing gear systems, control surfaces, and deployment mechanisms. The variable spring rate accommodates varying loads and shock absorption requirements during flight and landing.
Valve Actuation
In engines and machinery, conical springs are used in valve actuation systems.The variable spring rate allows for precise control of valve opening and closing, optimizing engine performance and efficiency.
Medical Devices
In medical equipment, conical springs are used in devices such as surgical instruments and prosthetics.The variable spring rate provides controlled force for delicate procedures and patient comfort.
Advantages of Using Conical Springs
Variable Spring Rate :
Conical springs offer a progressive force curve, providing softer initial compression followed by increased stiffness.
Space Efficiency :
The tapered design allows for efficient use of space in compact applications.
Precise Force Control :
The ability to tailor the spring rate along the length of the spring enables precise force control in various conditions.
Enhanced Performance :
Conical springs can improve the performance and stability of systems by adapting to changing loads and conditions.
Conclusion:
conical spring manufacturers in bangalore are specialized components that offer variable spring rates and precise force control in a wide range of applications. The manufacturing process involves precision forming, tapering, and heat treatment to achieve the desired performance characteristics. Understanding the manufacturing process and the applications of conical springs is crucial for engineers and designers to select the right components for their projects, ensuring optimal performance, efficiency, and reliability in mechanical systems.