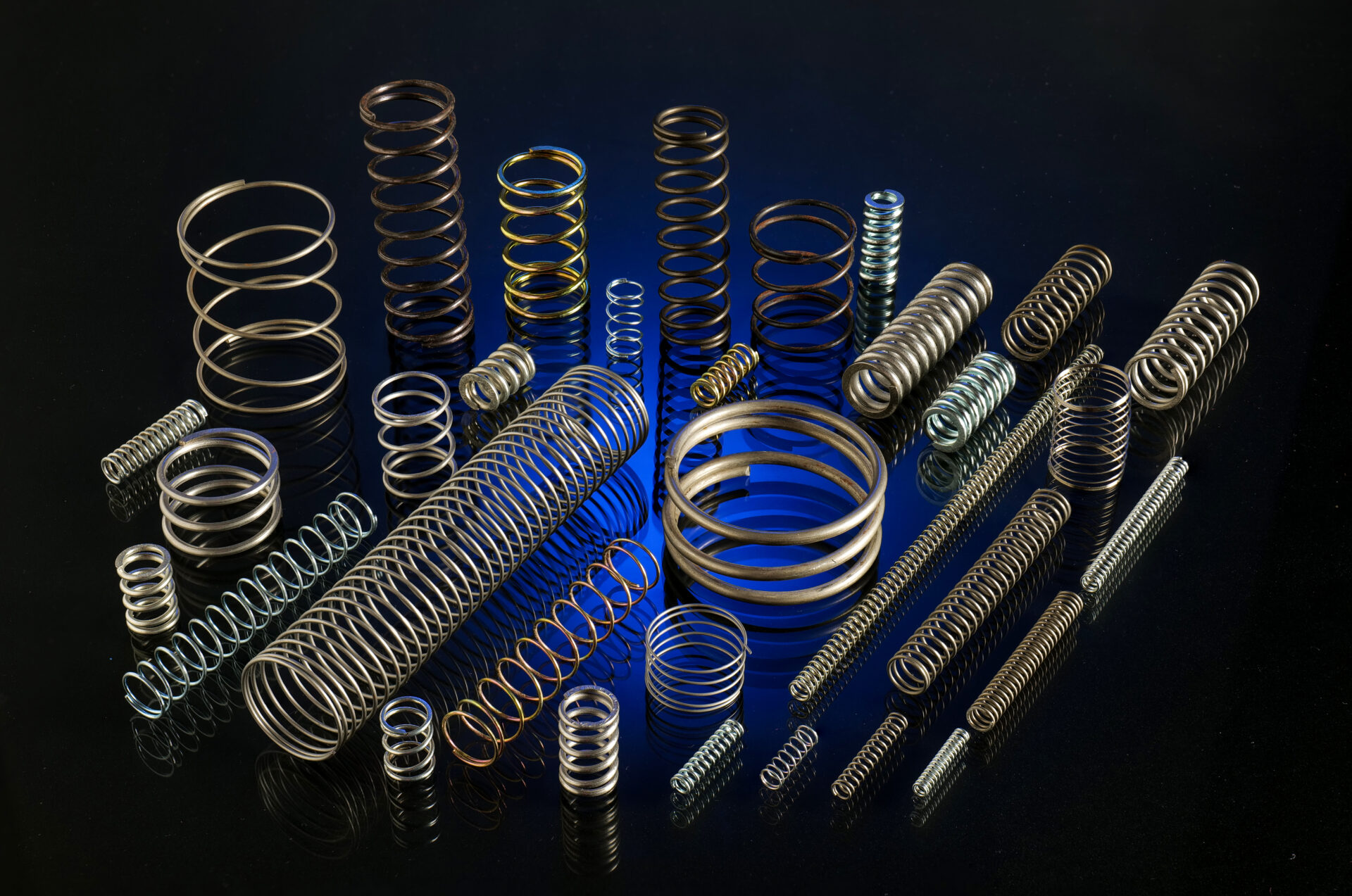
Compression Spring
Manufacturing Process of Compression Springs:
The process of compression spring manufacturers involves several steps to ensure precise dimensions, proper material properties, and reliable performance.
Material Selection :
- Compression springs are typically made from high-quality materials such as music wire, stainless steel, or high-carbon steel.
- The choice of material depends on factors such as required strength, resistance to corrosion, and the application environment.
Wire Forming :
- The process begins with a coil of wire that is fed into a machine.
- The wire is then formed into a coil shape by a coiling machine, which winds it around a mandrel to create the initial helical form.
Heat Treatment :
- After coiling, the compression spring undergoes heat treatment to improve its strength and durability.
- Heat treatment involves heating the spring to a specific temperature and then cooling it at a controlled rate.
- This process helps to set the spring’s shape, remove internal stresses, and enhance its mechanical properties.
Grinding (Optional) :
- In some cases, the ends of the compression spring may be ground to achieve flat or specific shapes.
- Grinding ensures uniformity and precision at the ends of the spring, facilitating proper seating and alignment in the application.
Shot Peening (Optional):
- Shot peening is a process where small, spherical particles are shot at the surface of the spring.
- This process induces compressive stresses on the surface, improving fatigue life and resistance to cracking.
Finishing :
- Compression spring manufacturers may undergo additional finishing processes depending on the application requirements.
- This can include coating or plating for corrosion resistance, painting for identification or aesthetics, or passivation for improved surface properties.
Quality Control :
- Throughout the manufacturing process, stringent quality control checks are essential.
- Dimensional measurements, tensile strength tests, and load testing are performed to ensure that each compression spring meets the required specifications.
Using Compression Springs
Compression spring manufacturers have a wide range of applications across industries due to their versatility and reliability
Automotive Industry
Compression springs are used in suspension systems, brake systems, and engine components. They provide the necessary force to absorb shocks, maintain tire traction, and ensure proper functioning of various automotive systems
Aerospace Industry
Compression springs are critical components in aircraft landing gear, control systems, and seat mechanisms. They offer the necessary force to support the weight of the aircraft, control flight surfaces, and provide comfort to passengers.
Industrial Machinery
In manufacturing machinery, compression springs are used in presses, stamping machines, and die assemblies. They provide controlled force for operations such as pressing, punching, and forming metal parts.
Medical Devices
Compression springs are used in medical devices such as syringes, surgical instruments, and implantable devices.They provide precise force for controlled movements, ensuring accurate dosing and safe operation.
Advantages of Using Compression Springs
Versatility :
Compression springs can be designed and manufactured in various sizes, shapes, and load capacities to suit specific applications.
Reliability :
Properly manufactured compression springs offer consistent performance over millions of cycles, providing long-term reliability.
Space Efficiency :
They can store a significant amount of energy in a compact space, making them ideal for applications with limited room.
Cost-Effective :
Compression springs are often cost-effective solutions for providing reliable force and energy storage in mechanical systems.
Conclusion:
Compression spring manufacturers in bangalore are indispensable components in a wide range of industries, providing controlled force, energy storage, and reliable performance. The manufacturing process involves precise steps from material selection to finishing, ensuring high-quality products that meet stringent specifications. Understanding the manufacturing process and the applications of compression springs is crucial for engineers and designers to select the right components for their projects, contributing to efficient, reliable, and safe mechanical systems.