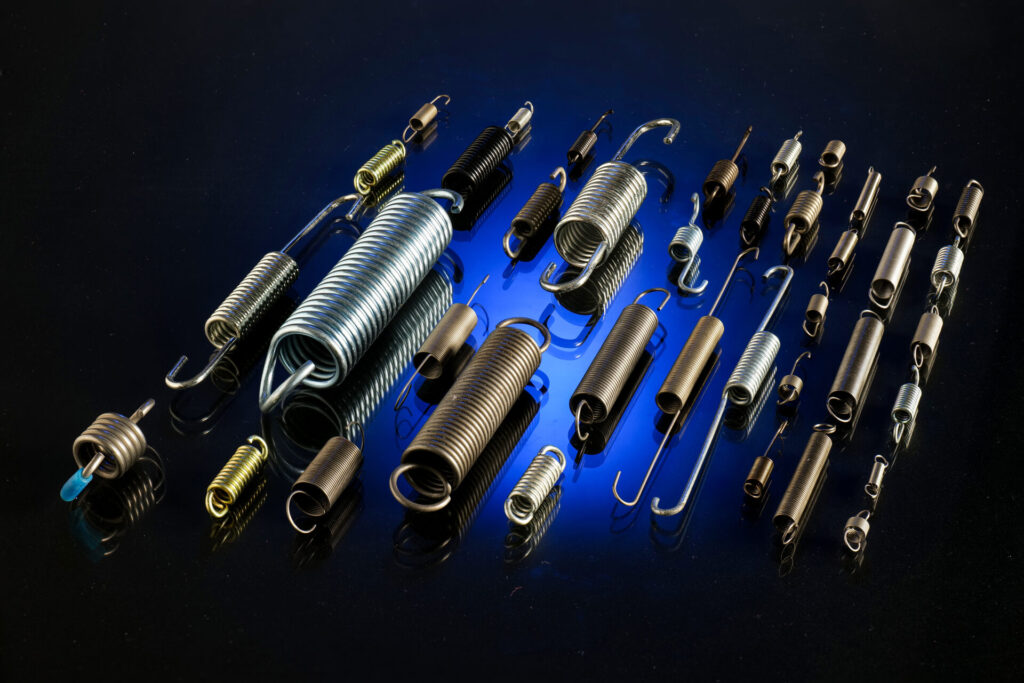
Tension springs
Manufacturing Process of Tension Springs :
The process of tension spring manufacturers involves several steps to ensure precision, durability, and reliability in their performance.
Material Selection:
- Tension springs are typically made from high-quality materials such as high-carbon steel, stainless steel, or music wire.
- The choice of material depends on the application, required strength, resistance to corrosion, and other factors.
Wire Forming:
- The process starts with a coil of wire that is fed into the manufacturing machine.
- The machine cuts the wire to the desired length based on the specifications of the tension spring being produced.
Coiling:
- The wire is then fed into a coiling machine, which forms it into the desired helical shape.
- The machine applies tension to the wire as it winds it around a mandrel, creating the coil that will become the tension spring.
Heat Treatment:
- Once coiled, the tension spring undergoes heat treatment to improve its strength and durability.
- This process involves heating the spring to a specific temperature and then cooling it at a controlled rate.
- Heat treatment also helps to relieve any internal stresses within the spring, ensuring it retains its shape and performance over time.
End Grinding:
- After heat treatment, the ends of the tension spring may be ground to achieve a flat or specific shape.
- Grinding ensures that the ends are uniform, allowing for proper attachment or fitting into the desired mechanism.
Finishing :
- Tension spring manufacturers may undergo various finishing processes depending on the application.
- This can include shot peening to improve fatigue life, plating or coating for corrosion resistance, or painting for identification and aesthetic purposes.
Quality Control :
- Throughout the manufacturing process, quality control checks are essential.
- Dimensional checks, tensile strength tests, and fatigue testing are some of the methods used to ensure that each tension spring meets the required specifications.
Using Tension Springs
Once manufactured, tension spring manufacturers find numerous applications across industries
Automotive Industry
Tension springs are used in vehicle suspension systems, clutch mechanisms, and braking systems.They provide the necessary tension for belts and chains, ensuring smooth operation of engines and other components.
Aerospace Industry
In aircraft, tension springs are vital for controlling flight surfaces, landing gear, and cargo doors. They must withstand extreme conditions while maintaining precise performance.
Industrial Machinery
Tension springs play a role in conveyor systems, agricultural equipment, and industrial robots. They provide tension to keep components in place or allow for controlled movement.
Medical Devices
Tension springs are used in various medical devices, such as surgical tools, prosthetics, and diagnostic equipment.They ensure precise movements and reliable operation in critical healthcare applications.
Advantages of Using Tension Springs
Versatility :
Tension springs can be customised to fit specific applications, thanks to various wire sizes, coil diameters, and end configurations.
High Performance :
They offer consistent force and reliable operation over millions of cycles, crucial for demanding applications.
Durability :
Properly manufactured tension springs are designed to withstand fatigue and harsh conditions, providing long service life.
Cost-Effective :
Despite their high performance, tension springs are often cost-effective solutions for mechanical systems.
Conclusion :
Tension spring manufacturers in bangalore use essential components in countless mechanical systems, providing the necessary force for operations ranging from automotive to aerospace. The manufacturing process involves precise steps to ensure quality, durability, and reliability. Understanding the manufacturing process and the applications of tension springs is crucial for engineers and designers to select the right components for their projects, ensuring optimal performance and safety.